Stereolithography: Revolutionizing 3D Printing Technology
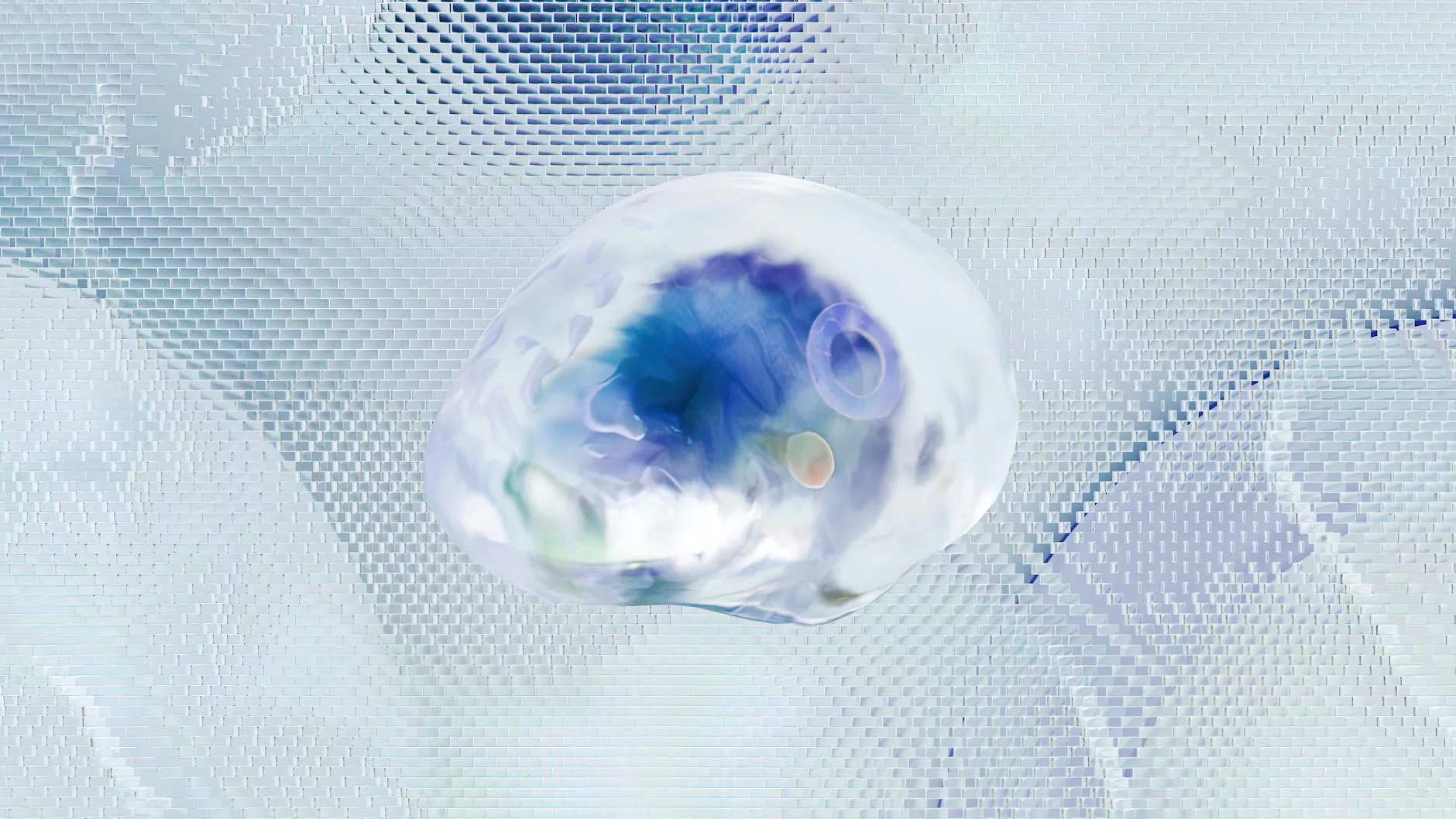
Stereolithography, often abbreviated as SLA, has significantly transformed the landscape of 3D printing since its inception in the 1980s. As one of the pioneering techniques in additive manufacturing, it has continuously evolved, leading to enhanced precision, speed, and versatility that makes it stand out in the realm of modern production processes.
Understanding Stereolithography
At its core, stereolithography is a method of 3D printing that utilizes ultraviolet (UV) light to cure and solidify layers of photopolymeric resin. This layer-by-layer approach allows for the creation of intricate designs and complex geometries, which are often impossible to achieve through traditional manufacturing methods.
How Stereolithography Works
The process of stereolithography involves several key steps:
- 3D Model Preparation: The journey begins with a 3D digital model created using CAD (Computer-Aided Design) software. This model serves as the blueprint for the final product.
- File Conversion: The CAD model is converted into a format compatible with the SLA printer, commonly STL (Stereolithography format), which defines the geometry of the part.
- Printing Setup: The SLA printer is configured, including the selection of the resin type, layer thickness, and print speed. The build platform is lowered into a vat of liquid resin.
- Layer Curing: A UV laser traces the outline of the first layer of the model. The light cures the resin, solidifying it. The platform then lifts slightly, allowing for a new layer of resin to flow beneath it.
- Post-Processing: Once the object is printed, it undergoes post-processing, which may involve additional curing, cleaning off excess resin, and, if needed, further finishing.
Benefits of Stereolithography
There are numerous benefits to using stereolithography in 3D printing:
- High Precision: SLA produces objects with incredible detail and surface finish, making it ideal for applications that require fine tolerances.
- Fast Production Times: The layer-by-layer approach allows for quick turnaround times, significantly reducing production lead times.
- Complex Geometry: Stereolithography can create intricate designs, enabling the manufacturing of complex parts that would be difficult or impossible to produce using traditional machining.
- Material Versatility: SLA printers can use a variety of resin types, including those with different mechanical properties, colors, and even flexibility.
- Eco-Friendly: Since SLA relies on photopolymerization, which uses UV light instead of heat, it can lead to lower energy consumption during production.
Applications of Stereolithography
From prototyping to production parts, stereolithography has been adopted across various industries:
1. Aerospace and Automotive
The aerospace and automotive industries utilize stereolithography for rapid prototyping and creating intricate components, such as:
- Air duct models
- Tooling patterns
- Complex engine components
2. Medical and Dental
In the medical field, stereolithography is vital for producing:
- Custom dental molds and implants
- Anatomical models for surgical planning
- Prosthetics tailored to individual patients
3. Consumer Products
Many consumer products, especially in the electronics and fashion sectors, benefit from SLA, allowing designers to:
- Create detailed prototypes for testing
- Utilize unique aesthetic designs that require fine details
Advantages Over Other 3D Printing Methods
Stereolithography isn’t the only 3D printing technology available, yet it reigns supreme in several areas:
- Superior Finish: Compared to technologies like FDM (Fused Deposition Modeling), SLA produces parts with a smoother surface finish straight off the printer.
- Dimensional Accuracy: SLA offers high dimensional accuracy and can hold tolerances of ±0.1mm or better.
- Material Properties: Stereolithography resins can emulate the properties of various materials, making them suitable for diverse applications.
Challenges and Considerations
Despite its many advantages, stereolithography has some challenges that need to be considered:
- Material Cost: The photopolymer resins used in SLA can be more expensive than filament used in other printing technologies.
- Post-Processing Needs: Parts often require cleaning and curing, which can add time and labor to the production process.
- Limited Build Size: SLA printers typically have smaller build sizes compared to some other 3D printing technologies, limiting the dimensions of the parts that can be produced.
The Future of Stereolithography
The future of stereolithography looks promising as advancements continue to drive innovation. Developments in materials science are leading to:
- Higher Performance Resins: New formulations are being introduced that offer improved mechanical properties and durability.
- Speed Enhancements: Innovations in printing technology, such as the use of advanced laser systems, are reducing print times even further.
- Integration with Industry 4.0: The incorporation of IoT and AI in stereolithography processes will streamline operations and enhance quality control.
Conclusion
Stereolithography has firmly established itself as a cornerstone in the world of 3D printing, offering unparalleled precision, speed, and versatility. As industries continue to evolve and demands for innovation rise, SLA technology will undoubtedly play a critical role in shaping the future of manufacturing. Whether you’re a designer, engineer, or manufacturer, understanding and leveraging the potential of stereolithography will empower you to stay ahead in this fast-paced marketplace. For those looking to explore the capabilities of stereolithography, visiting platforms like infotron.com.tr can provide access to cutting-edge resources and insights.