Understanding Plastic Injection Mold Companies: A Comprehensive Guide
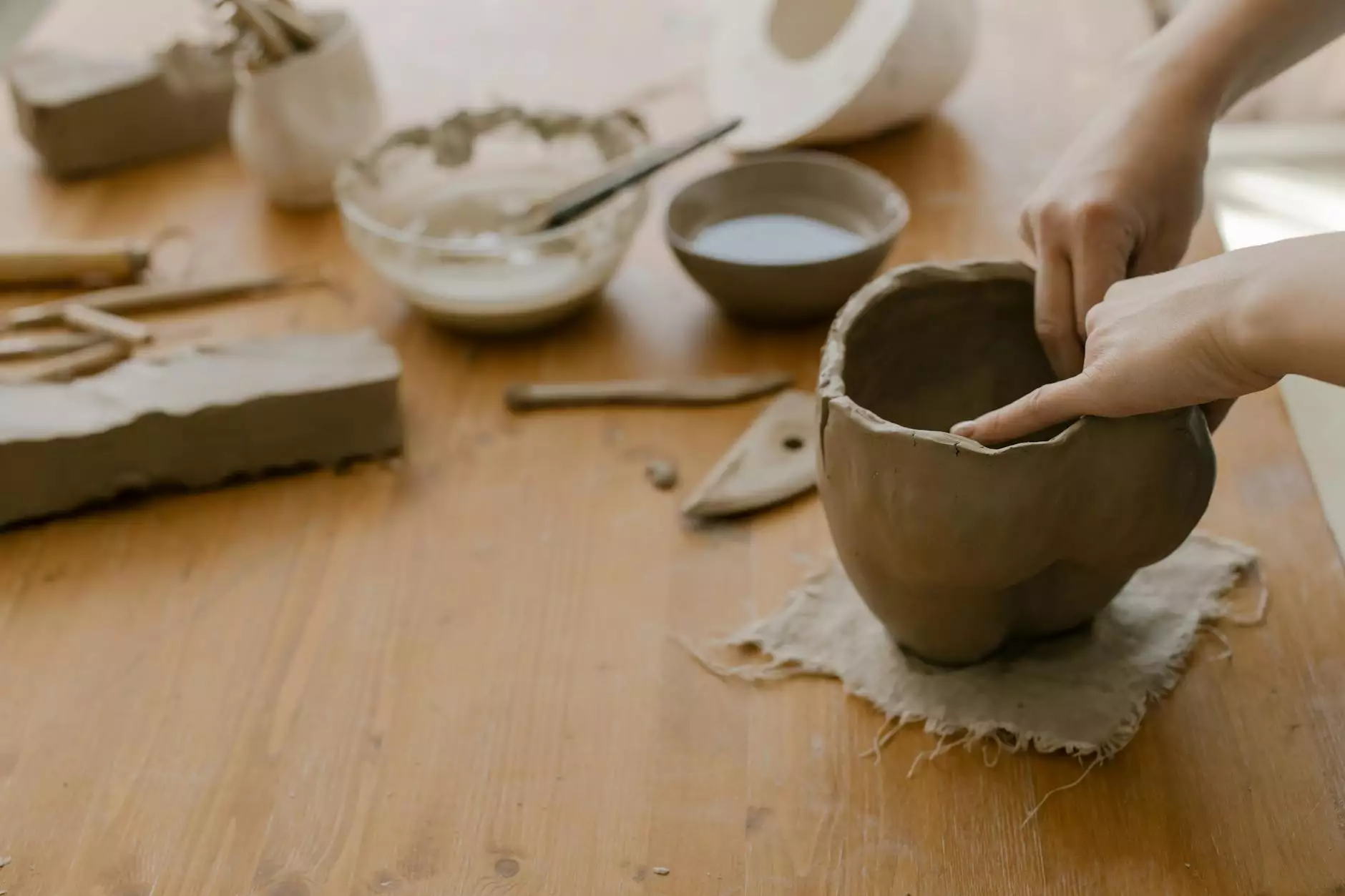
In today's rapidly evolving manufacturing landscape, plastic injection mold companies are playing an increasingly vital role. These companies specialize in producing high-quality plastic components and products that are essential in various industries, including automotive, electronics, and consumer goods. This article delves deep into the world of plastic injection molding, explaining its processes, benefits, and why it is integral to modern manufacturing.
What is Plastic Injection Molding?
Plastic injection molding is a manufacturing process that involves the injection of molten plastic into a mold to create parts and products. This process is favored for its efficiency in producing large quantities of high-quality plastic components. The process typically includes several key steps:
- Material Selection: The first step involves choosing the right type of plastic, which can be thermoplastic or thermoset polymer, depending on the application.
- Mold Design: Engineers design a mold that is precise in shape and dimensions to ensure that the final product meets specifications.
- Melting and Injection: The selected plastic is heated to a molten state and injected into the mold under high pressure.
- Cooling: The molten plastic is allowed to cool and solidify within the mold.
- Demolding: Once cooled, the mold opens, and the finished part is ejected.
The Role of Plastic Injection Mold Companies
Plastic injection mold companies are essential to the manufacturing ecosystem. They provide a range of services that go beyond mere production:
1. Design Services
Many plastic injection mold companies offer comprehensive design services, working alongside clients to develop custom solutions. The design process typically involves:
- 3D modeling to visualize the part before production.
- Prototyping to test functionality and fit.
- Iterative design to refine based on client feedback.
2. Prototype Development
Prototyping is a crucial step in the injection molding process. Companies create prototypes that allow clients to evaluate design and functionality before committing to mass production. This process helps to identify potential flaws early, saving time and resources.
3. Mass Production
Once a design is finalized, plastic injection mold companies use their advanced machinery to produce large quantities of the designed parts efficiently. Their ability to scale production means that businesses can meet market demand quickly, which is particularly crucial in fast-paced industries.
Advantages of Working with Plastic Injection Mold Companies
Choosing to partner with plastic injection mold companies presents numerous advantages:
- Cost-Effectiveness: With the ability to produce thousands of parts in a single run, the cost per unit decreases significantly, making it an economical choice for mass production.
- High Quality: Injection molding allows for high precision and repeatability, ensuring that the components meet stringent quality standards.
- Material Versatility: A wide range of plastics can be used, allowing for the production of different products according to specific requirements.
- Enhanced Efficiency: Modern machines and techniques streamline the production process, reducing waste and turnaround times.
Types of Plastic Injection Molds
Plastic injection mold companies utilize various types of molds depending on the production needs and complexity of the parts:
1. Single Cavity Molds
This type of mold produces one part per cycle, which is suitable for low-volume production runs.
2. Multi-Cavity Molds
Multi-cavity molds can produce several identical parts in a single cycle, enhancing productivity and reducing costs for larger orders.
3. Family Molds
Family molds allow different parts to be produced simultaneously, which is beneficial for manufacturers needing multiple products with similar features or components.
Applications of Plastic Injection Molding
The applications for products created through plastic injection molding are vast and varied. Here are some of the most common sectors that benefit:
- Automotive Industry: Car components such as dashboards, bumpers, and trims are often produced using plastic injection molds.
- Consumer Electronics: Many electronic devices use plastic components for housings and connectors, showcasing the versatility of the injection molding process.
- Healthcare: Medical devices and components often use specially formulated plastics to meet regulatory compliance and safety standards.
- Household Goods: Everyday items like containers and kitchen tools frequently utilize custom plastic parts manufactured through injection molding.
Choosing the Right Plastic Injection Mold Company
Selecting a plastic injection mold company is a critical decision that can impact your project’s success. Here are some factors to consider when making your choice:
1. Experience and Expertise
Look for companies with a proven track record in the industry. A wealth of experience translates to superior expertise in handling complex projects and troubleshooting potential issues.
2. Technology and Equipment
Advanced technology and up-to-date machinery can significantly influence production quality and efficiency. Companies that invest in the latest technology often deliver better results.
3. Quality Assurance
Inquire about the quality control processes the company employs. Robust quality assurance measures ensure that the final products are consistent and meet required specifications.
4. Customer Support
Reliable customer service can significantly enhance your experience. The right company should offer comprehensive support throughout the design, production, and delivery processes.
Future Trends in Plastic Injection Molding
The future of plastic injection molding looks promising, driven by technological advancements and a growing demand for sustainable practices:
1. Sustainability in Materials
There’s a rising trend towards using biodegradable and recycled materials for plastic products. Companies are exploring innovative material options to reduce environmental impact.
2. Automation and Smart Manufacturing
With advancements in AI and robotics, plastic injection mold companies are likely to adopt more automated systems, enhancing precision and reducing labor costs.
3. 3D Printing Integration
Some companies are beginning to integrate 3D printing with traditional injection molding for rapid prototyping, which streamlines the design process and decreases time to market.
Conclusion
In conclusion, plastic injection mold companies are indispensable partners in the manufacturing sector, providing essential services that drive innovation and efficiency. Their expertise in utilizing advanced technology to produce high-quality, precise, and cost-effective plastic components makes them vital players across various industries.
As industries continue to evolve and adapt, the role of plastic injection molding will expand even further, underscoring the significance of choosing the right partner. For businesses looking for reliable solutions in plastic production, Deep Mould is committed to delivering excellence through its experienced team and cutting-edge technology.